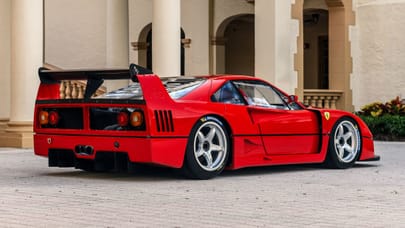
Want to see how Tesla builds its cars?
Includes: robots, robats, and the largest stamp press in America
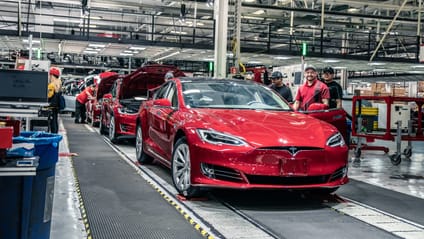
Tesla’s Fremont behemoth, where all Model X, Model S and Model 3s are built, has to be one of the most famous car factories in the world - formerly for all the wrong reasons, more recently for all the right. The home of “production hell,” in Elon’s words, it’s where a previously boutique electric car company had to teach itself how to manufacture on a mass scale, in full view of the world.
As recently as last year, there were more bottlenecks here than the Coca-Cola factory up the road in Sacremento. Build quality was under fire, delays were rife, share price was sliding and there was no sign of the hallowed $35,000 Model 3, or whether it would ever be possible. Lately, though, things are looking up.
Through a combination of ruthless streamlining, reducing the level of automation in some key areas, and the boss himself resorting to sleeping on the factory floor to get the log-jams sorted, the Teslas are starting to flow, and so is the profit. In 2018 Fremont spat out 254,530 cars, 152 per cent more than in 2017, and Musk insists the trajectory is right to produce 500,000 in 2019. That’s 10,000 a week.
Recently, Top Gear embarked on a marathon Tesla-based 24 hours – road-tripping from San Francisco to Los Angeles in a Model 3 Performance and attending the reveal of the new Model Y, but before all that we had a chance to tour the Fremont factory. You can watch the video of the entire day, but it was the factory that left the deepest impression. So here’s a gallery of what we found inside, along with some mind-scrambling numbers for good measure. Here we go…
Advertisement - Page continues belowWith such juicy employee discounts on the cars, row upon row of destination chargers line the factory lot. How long until all car parks look like this?
Safety cap, eye protection, ear plugs and steel-toe footwear all mandatory on the factory floor. Posing for a photo like an idiot, optional.
Advertisement - Page continues belowElectric motors awaiting their new homes inside S, 3, or X. Fremont factory currently covers 5.3 million square feet of manufacturing and office space on 370 acres of land – or to use more familiar units, about 185 football pitches.
And it’s about to get a whole lot bigger. Tesla’s expansion plans, approved in 2016, mean it will eventually double in size.
Before Tesla picked it up for the bargain price of $42m in 2010, the facility was home to GM from 1962 to 1982, then GM and Toyota’s New United Motor Manufacturing (NUMMI) partnership from 1984 until 2009.
Model 3’s fully-automated three-stage stamping press. The first makes the shape, the second trims the edges, the third punches the holes.
Advertisement - Page continues belowInspecting door panels coming off the press. Over 10,000 Tesla employees work at the Fremont factory, plus nearly 5,000 contractors.
Since buying the factory in 2010 Tesla has spent over $3 billion on developing it.
Advertisement - Page continues belowBest bit about the tour? You get to ride in this golf-buggy train thing, driven by the world’s most enthusiastic guide.
Model S body-in-white being tugged along by an autonomous robot, programmed to follow the black line on the floor.
Model 3s fly overhead. In the same amount of space that it takes to build 50,000 Model Ss, Tesla can build 250,000 Model 3 vehicles. Model 3 line known as ‘the brick’.
Robots on the Model 3 body line. Floor mounted arms are ‘robots’, the upside-down ones known as ‘robats’. Geddit?
Model 3 battery from the Giga factory in Nevada plugs into motors, suspension and brakes before being married to the finished body 50 metres further down the line.
One of the biggest metal presses in North America, that red cube weighs in at 500 tonnes, and stamps out entire body sides for the Model S.
Scoop! Tesla is working on a flying car. Well, you wouldn’t put it past him, would you?
Ta-da! The point where full-formed Model S and X roll off the production line.