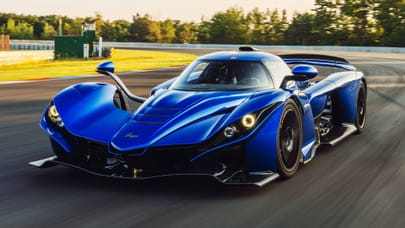
BMW refuses to close the door on hydrogen power
Its halo Munich plant remains flexible to fuels beyond electric, while also utilising ever more AI
BMW recently announced its latest step on the road to full electrification, namely that its flagship Munich factory will exclusively produce EVs from 2027.
However, a chat with board member Milan Nedeljković confirmed that the new assembly line under construction will remain flexible to alternative fuels – not least hydrogen, a path BMW continues to forge with its fleet of iX5 prototype mules.
“Hydrogen remains an important alternative,” he tells TopGear.com. “That’s why we have a fleet of hydrogen cars out testing and why we’re working intensively on improving the technology further. Alternatives need to be considered; that’s why we keep our facilities flexible to hydrogen and to other technologies.
“We won’t invest in internal combustion technology if there are no new combustion engines coming, but it’s crucial that we stay flexible on the production line for whatever may come.”
The new assembly hall will host the second of BMW’s new Neue Klasse models, a saloon whose 2026 debut comes a year after an SUV that’ll be made in Hungary. Has BMW symbolically saved the four-door as a more purist, traditional car to roll out of its Bavarian birthplace?
“The 3 Series has become ‘the product of Munich’ and we will have this new limousine from the Neue Klasse here, but it’s a coincidence that works nicely for historical reasons,” smiles Nedeljković.
“Likewise, our new assembly building is not because of Neue Klasse, but because it’s the original from 100 years ago [when BMW made aeroplane engines in Munich] so we needed a new facility. So why not also build it for the new technology? It’s a benefit to bring a new facility and new model line together.”
With some inevitability the new facility will lean more heavily into Artificial Intelligence than ever, but factory boss Peter Weber assures us AI has already been utilised very neatly at Munich – and that it’s being used to support rather than replace the plant’s 7,800 employees.
“Many employees will work on 500 cars within their shift,” he says. “To ensure they do it with premium quality, it’s fundamental that every worker knows their procedure off by heart. Training methods are the most decisive factor in achieving quality.
“Our apprentices now learn to weld using Augmented Reality. Before touching any metal, they learn their gun technique and speed of process in an AR environment. As soon as they pass in AR, they can do the job in reality. Digitalisation is a big lever for our people to perform their job in the most robust way.”
Top Gear
Newsletter
Thank you for subscribing to our newsletter. Look out for your regular round-up of news, reviews and offers in your inbox.
Get all the latest news, reviews and exclusives, direct to your inbox.
AI, he says, is used to ensure detail quality in BMWs, from ensuring their badges are fitted with micrometric accuracy to the roof antennae being glued perfectly.
“We’ve already implemented more than 70 quality gates based on AI,” Peter tells us, “just using standardised hardware and software. People are asking for it. They know the most critical production processes and are asking for our support. If we give our robots AI, they gain another sense. It allows our transport robots to manoeuvre more safely.
“It is our basic belief that digitalisation, comprising AI, is focused on supporting our people and supporting our processes.”