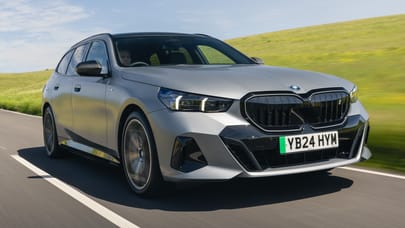
This is how spoked wheels are made
Wheels. Bloody brilliant things, aren’t they? Aside from being crucial elements of making any car or motorbike move, they’re also a cylindrical canvas that can be made into art.
Though, have you ever appreciated the effort that goes into making a wheel? Especially a classic, spoked motorbike wheel? I hadn’t. Until the other day…
As part of our ongoing custom Royal Enfield motorbike project, I ventured to Britain’s bellybutton, Birmingham, to see some proper heavy machinery and hand-built magic as we made some shiny new wheels at Central Wheel Components. CWC has been making motorbike wheels for pretty much every motorbike you can think of since 1897. So they know a thing or two about them. And the process is fascinating.
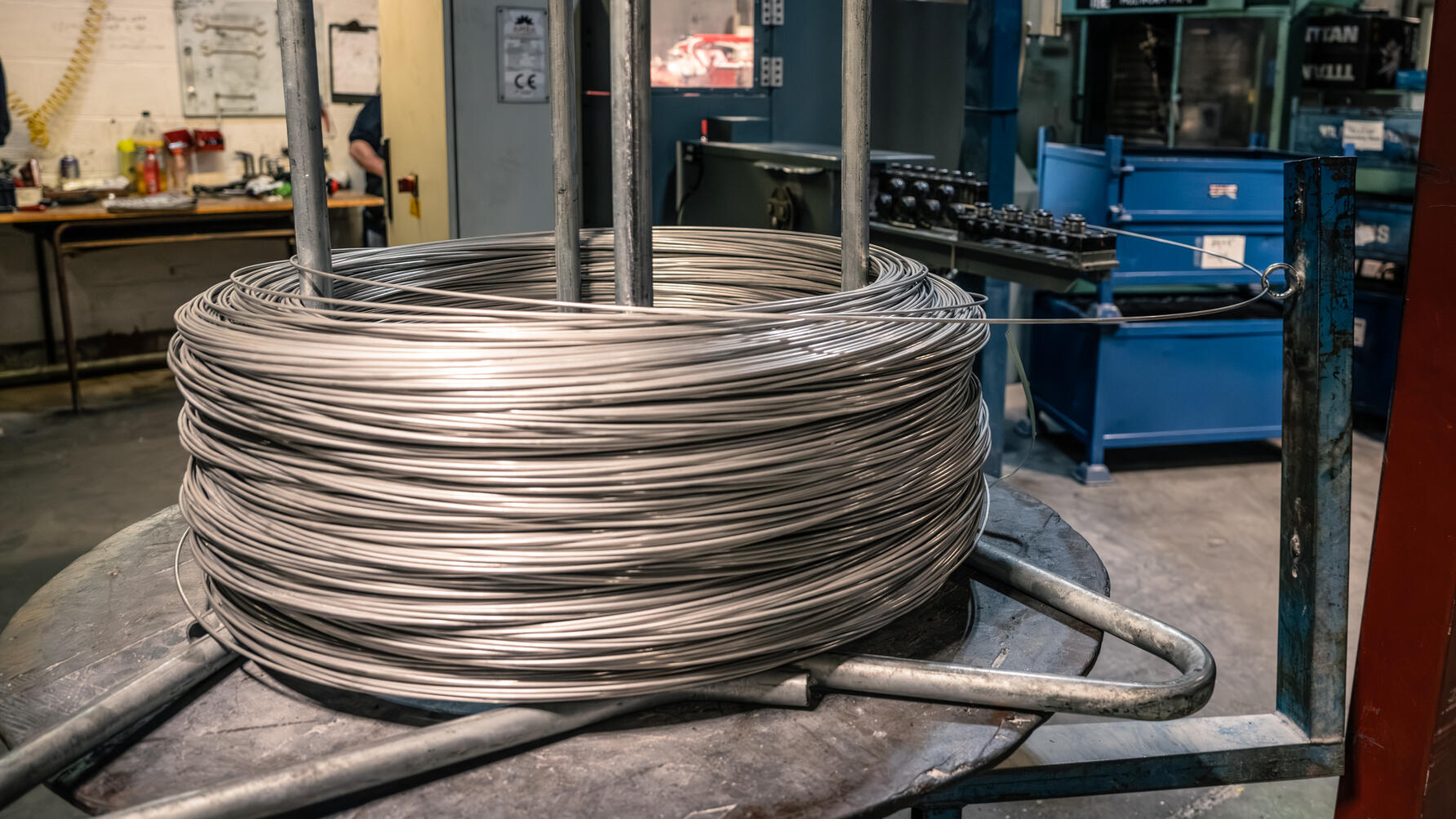
First, a large reel of stainless-steel wire (good for 35,000 spokes) is fed into a machine to be straightened, cut to length, bent and threaded. It’s all satisfyingly loud and clattery work as two machines argue away, chomping and clanging away at each other, spitting out 100 spokes a minute. Once the spokes are made, beautiful aluminium rims are then selected off the rack and punched by hand. Working around the rim, each dimple is identified, eyed up and lined up to the correct angle to work with the offset and hub. ‘Millsy’, one of CWC’s veterans, has been doing this for 37 years, so has a laser guided eye for it.
After that, Millsy hands the rim and spokes to his mate down the line, Chris – a lovely man and a sort of wheel Yoda. He laces up the wheel in what looks like the most complex game of Pick-Up Sticks ever. Criss-crossing the spokes correctly is easier than it looks, with each one being secured to the rim with brass nipples before the bearings are re-inserted into the hub. Then it's thrown over to Steve.
Steve is a machine. Literally. He ‘trues’ the wheel – that’s the process of sorting the alignment once it’s been built so the rim is central to the hub. Using some sort of superpower, Steve adjusts any radial (up and down) and axial (side to side) imperfections by slackening some spokes and tightening others. It's a great skill requiring superhuman patience as he torques the spokes up by feel and does the alignment by eye. With decades of practice it’s the kind of kinaesthetic magic that a robot can’t do, a uniquely satisfying hand-craftsmanship that’s a joy to watch.
So that’s how you make a wheel. What are we going to throw on the Enfield?
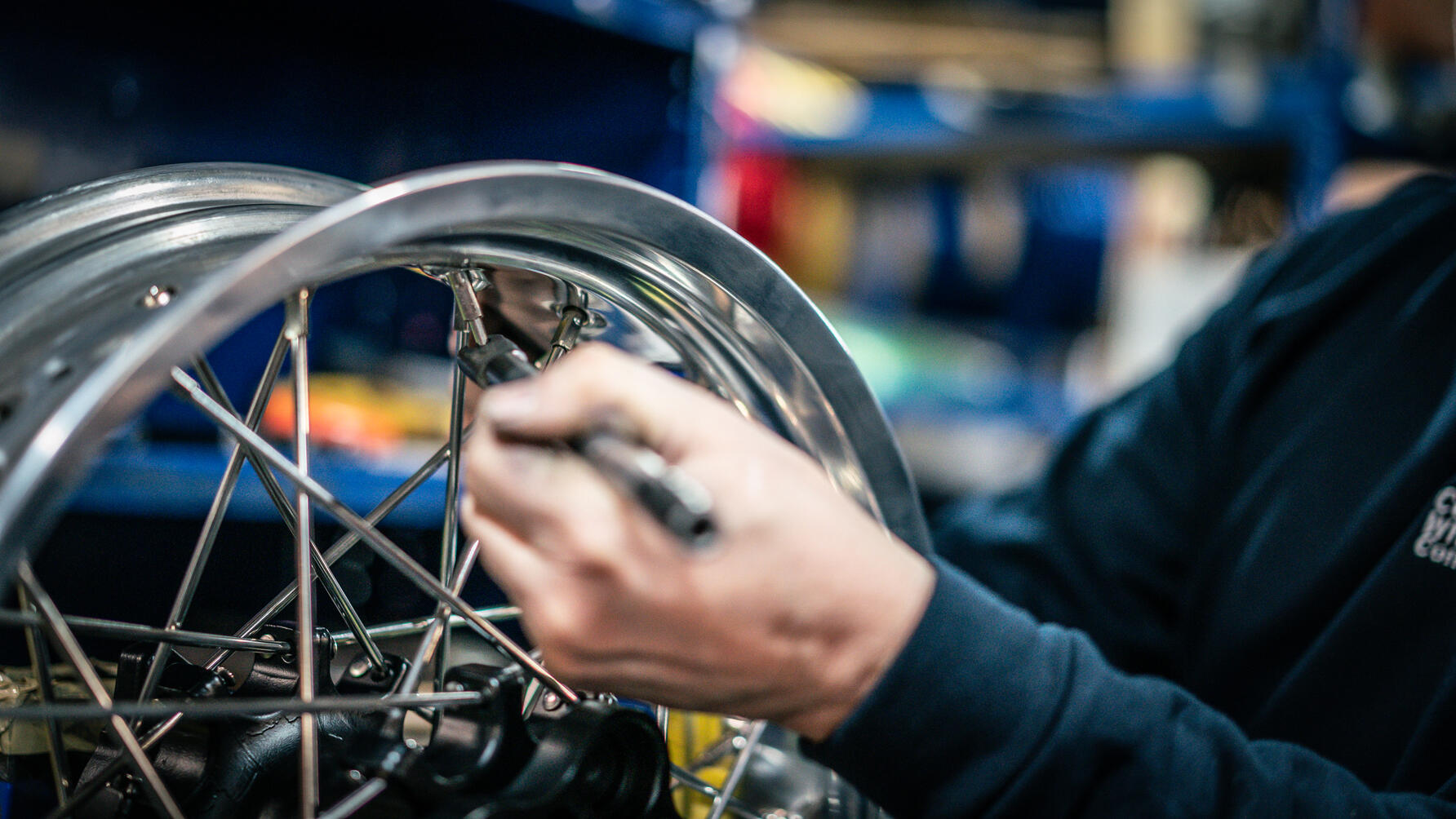
Given that CWC’s main business is supplying motocross wheels, the level of customisation you can get them to provide is crazy. Pretty much any component from the hubs, spokes, rims and nipples can be painted or ceramic coated in whatever colour you want. You can even apply fades, blends or have them laser etched if you’re feeling particularly trick. We’ve not done any of that. For reasons that’ll become clear down the line, we want a classic look, one that mimics an old BBS motorsport rim. So CWC have made up a new wheel which keeps the same style as standard (a 36-hole rim, 8 gauge spikes with a 14 degree bend) but they’re now polished and slightly swollen to give a tougher look. Oh, and now wrapped in a wider, stickier Bridgestone Battlax BT46 tyre which should increase our general performance (especially in the wet) but also make the bike more comfortable while doing bigger miles.
Tell us what your favourite wheel design is below. And let us know what you think of our new rims while you're there.
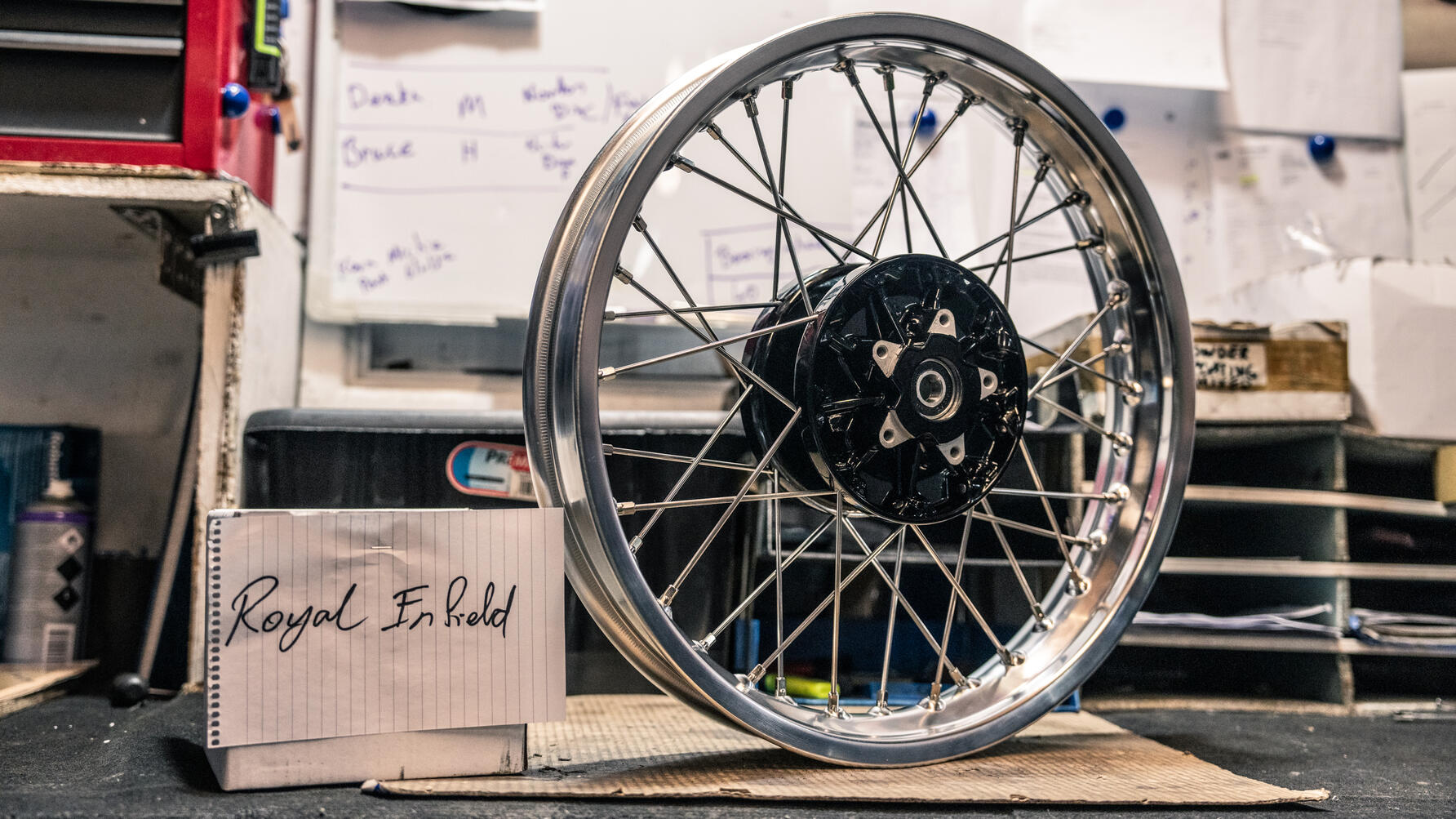
Featured
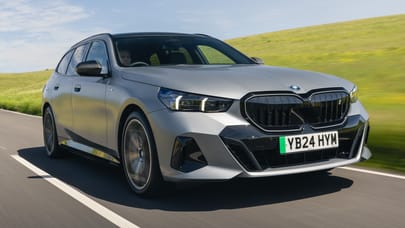
Trending this week
- Top Gear's Top 9
Nine of the weirdest American pickup trucks